Why do electric motors fail?
Despite being increasingly efficient and reliable, modern electric motors are vulnerable to a number of issues, including:
- Overload: when the motor’s capacity or load is exceeded, the resultant heat and excess current draw can cause premature wear to the motor’s electrical and mechanical components, including degradation of the motor winding insulation.
- Overheating: one of the most common causes of electric motor failure, overheating can occur due to excessive current and/or poor ventilation. Even a couple of extra degrees can cause premature wear to the motor’s components.
- Transient voltage: short power surges from internal or external sources can create transient voltages on distribution systems. Varying in both frequency and amplitude, these can breakdown motor winding insulations, leading to premature motor failure.
- Reflections on PWM signals: variable frequency drives use pulse width modulation (PWM) to control the motor’s output. If these are not installed or maintained correctly, it can result in a reflection, whereby some of the signal travels back to the source. This can cause an impedance mismatch, putting more strain on the motor winding insulation.
- Misalignment: if the drive shaft is not properly aligned with the load, harmful forces can be passed along the shaft and into motor, causing excess wear and increasing the motor’s load. It can also create vibrations, that wear down components.
- Imbalance: an imbalance in load distribution can result in excessive current flow across one or more phases. The additional stress in each of the circuits can increase operating temperatures, which in turn can breakdown the motor’s winding insulation.
- Bearing wear: failed bearings due to normal wear and tear, lack of lubrication, overloading etc can result in increased drag and heat, putting more strain on, and accelerating the wear of, other components.
- Moisture and humidity: electrical machinery and water do not mix. Excess moisture can damage the electric motor’s insulation and corrode shafts, rotors and bearings, both reducing the motor’s lifespan.
- Harmonic distortion: other sources of high-frequency AC voltage or current can disrupt the performance of the motor. Instead of using the additional energy to turn the motor, it is distributed to windings and bearings, causing internal energy losses. Over time the resultant heat, will reduce the insulation of the windings.
- Contamination: contaminants such as dust, dirt or other abrasive particles can find their way into the motor, where they will slowly erode and wear key components.
- Wear and tear: like any mechanical device, electric motors will wear overtime, eventually leading to failure.
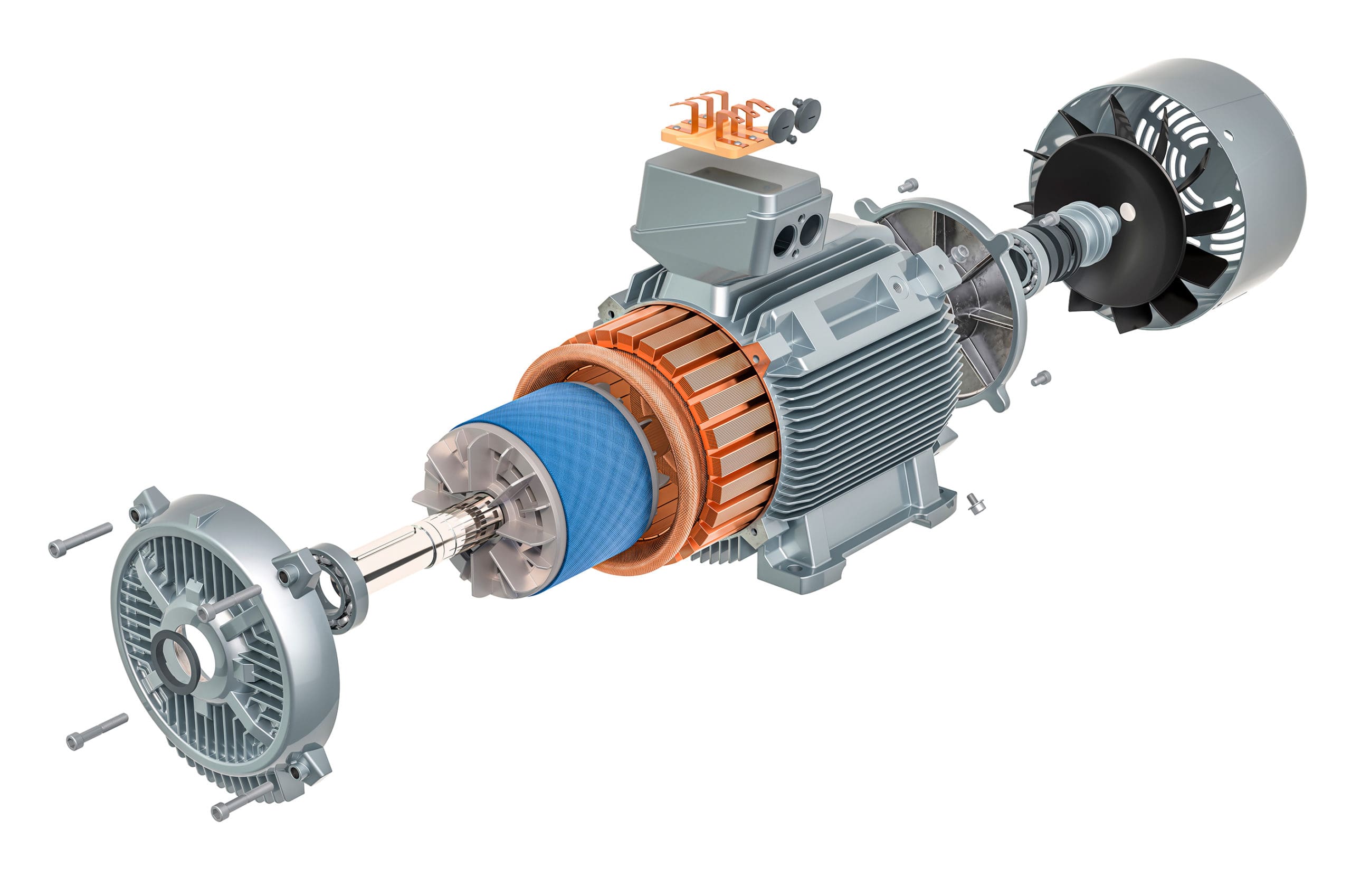
What are the symptoms of a faulty electric motor?
The tell-tale signs of a faulty electric motor include:- Unusual noises: often one of the first signs, strange noises such as rattling, grinding or humming when the motor is running, can indicate issues with bearings, gears and other components.
- Vibrations: similarly, unusual vibrations may be a sign of wear to the bearings and misaligned or loose components.
- Overheating: if the motor is hot to the touch or the paint is darker in the centre of the motor casing, it’s likely to be excess heat.
- Reduced performance: a reduction in speed, power output or efficiency can signal both mechanical or electrical problems.
- Strange smells: a burning or smell coming from the motor could suggest overheating or a breakdown of the winding’s insulation.
- Physical damage: visible signs of damage of to the outer casing, wiring or other components can indicate underlying issues.
- Increased energy usage: motors about to fail, will often consume more power than usual, without any increase in load etc.
- Frequent tripping: if the electric motor frequently trips circuit breakers or blows fuses, then there may be an electrical fault due to excessive draw, short circuits or insulations issues.
- Smoke or sparks: any smoke, sparks, or arcing during operation can point to electrical issues, that will need addressing asap.
How to troubleshoot a faulty electric motor?
Whilst you should always refer to the manufacturer’s guidance for the specific motor you are working on, following these steps will help streamline your diagnosis. Note only qualified technicians should undertake this work:
- Visual inspection: start by carefully the checking the motor and its surroundings for obvious damage such as dents to the housing, loose, damaged or corroded connections, signs of overheating etc.
- Check the bearings: if possible, rotate the shaft by hand to check for sign of wear and damage – too much play, noise or rough movement, which could indicate bearing issues.
- Test the power supply: ensure that the motor is receiving the right voltage and that the power supply is stable. Use the appropriate equipment to measure the voltage at the motor terminals.
- Listen and feel: whilst the motor is running, listen for any unusual sounds such as rattling, grinding or humming. Similarly feel for vibration – too much can indicate worn bearings, unbalanced loads or misalignment issues.
- Check the temperature: use a temperature probe or a thermal imaging camera to check for hotspots on the motor – this can indicate overheating or electrical issues.
- Measure the current draw: measure the motor’s current draw against its rated current to check for overloading.
- Test the capacitors: if the motor uses capacitors, check they are within tolerance using the right equipment.
- Test insulation resistance: with a megohmmeter, test the insulation resistance between the motor windings and frame – a noticeable decline in resistance could indicate a breakdown in the winding’s insulation.
- Test the motor’s load: disconnect the motor from the load and run it under no-load conditions to assess its performance.
- Check the harmonic distortion: use a power quality analyzer to measure the electrical current and temperature at the transformer. If the readings are out of spec, this suggests the motor is overstressed.
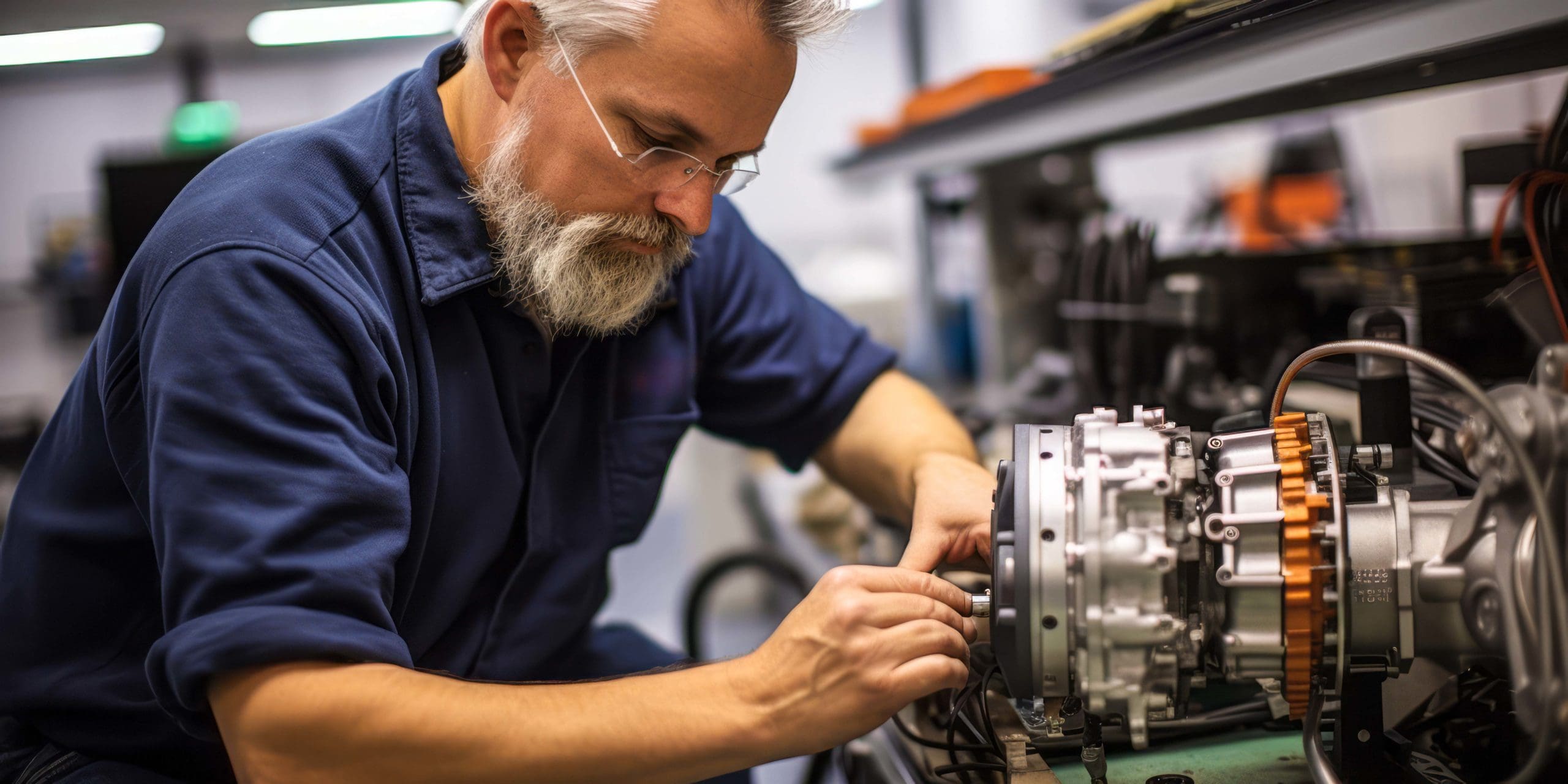
By following a structured approach to your diagnosis, qualified technicians will be able to quickly pinpoint issues and take remedial action to repair or replace the motor, as needed. If you don’t’ have the right skills and are unsure about what to do, our factory-trained professionals can diagnose, maintain and repair a full range of auto electrical systems. Click to learn more about our auto electrical services. We also offer a full repair and rewind service for all types, makes and age of rotating electric device, including electric motors For more.